Wie Kohlefaser-Automobilteile mit einem Autoklaven hergestellt werden
Die Herstellung von Kohlefaser Kfz-Teile Die Verwendung eines Autoklaven ist ein ausgeklügeltes Verfahren, das eine hohe Festigkeit und leichte Eigenschaften gewährleistet. Im Folgenden finden Sie die detaillierten Schritte dieser Herstellungsmethode:
1. Vorbereiten des Kohlefaser-Layups
Der Prozess beginnt mit der Vorbereitung des Kohlefaser-Layups. Kohlefasergewebe oder Prepreg (mit Harz vorimprägniert) wird je nach Teiledesign in bestimmte Formen und Größen geschnitten. Die Schichten aus Kohlefaser werden sorgfältig in einer Form angeordnet, um die gewünschte Dicke und die gewünschten strukturellen Eigenschaften zu erreichen. Dieser Schritt ist von entscheidender Bedeutung, da er die Festigkeit und Leistung des endgültigen Teils bestimmt.

2. Laden in die Form
Sobald das Kohlefaser-Layup vorbereitet ist, wird es in eine Form gelegt, die die Form des Automobilteils definiert. Die Form ist so konzipiert, dass sie den hohen Drücken und Temperaturen im Autoklaven standhält. Die Kohlefaserschichten werden sorgfältig in der Form positioniert, um eine korrekte Ausrichtung zu gewährleisten und Defekte oder Lufteinschlüsse zu vermeiden.
3. Einlegen in den Autoklaven
Die Form, in der sich das Kohlefaser-Layup befindet, wird dann in den Autoklaven gelegt. Ein Autoklav ist ein Hochdruckbehälter, der gleichzeitig Wärme und Druck ausüben kann. Dieser Schritt ist entscheidend für den Aushärtungsprozess der Kohlefaser.
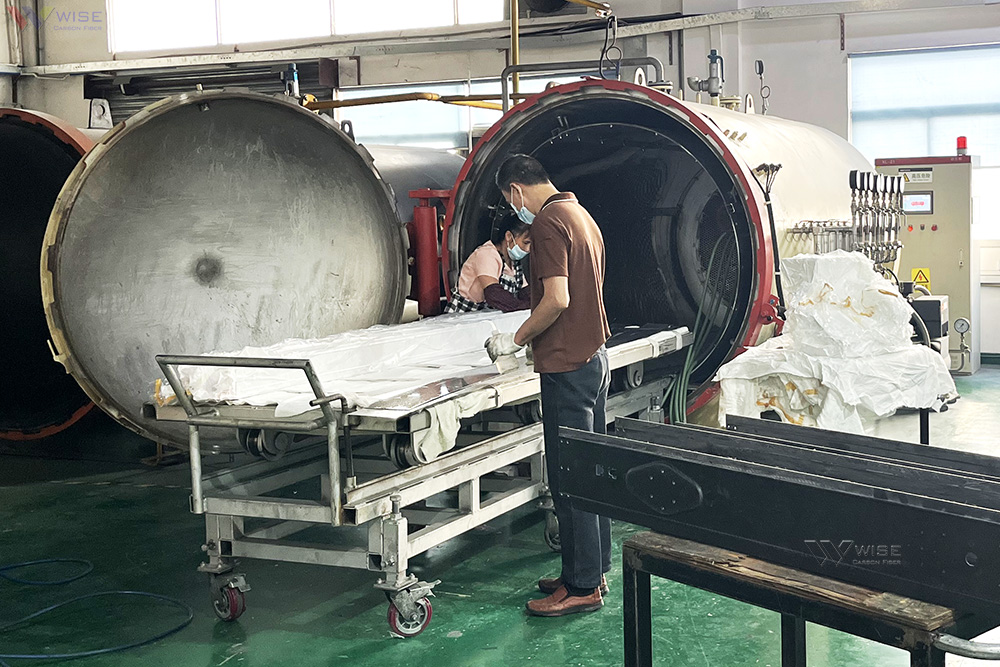
4. Hitze und Druck ausüben
Im Inneren des Autoklaven wird die Temperatur schrittweise auf das erforderliche Niveau erhöht, in der Regel zwischen 120 °C und 180 °C (248 °F bis 356 °F), abhängig vom verwendeten Harzsystem. Der Druck wird ebenfalls erhöht und liegt typischerweise zwischen 50 psi und 100 psi. Die Kombination aus Hitze und Druck lässt das Harz fließen und die Kohlefaser vollständig imprägnieren, wodurch eine starke Verbindung zwischen den Fasern gewährleistet wird.
5. Aushärtungsprozess
Beim Aushärtungsprozess werden Temperatur und Druck für eine bestimmte Dauer, in der Regel mehrere Stunden, aufrechterhalten. Während dieser Zeit durchläuft das Harz eine chemische Reaktion, die dazu führt, dass es aushärtet und aushärtet, wodurch ein fester Verbundwerkstoff entsteht. Die kontrollierte Umgebung im Autoklaven stellt sicher, dass der Aushärtungsprozess gleichmäßig ist, was zu einem qualitativ hochwertigen Teil mit optimalen mechanischen Eigenschaften führt.
6. Kühlen und Entformen
Nach Abschluss des Aushärtungsprozesses wird der Autoklav schrittweise auf Raumtemperatur abgekühlt. Anschließend wird die Form aus dem Autoklaven entnommen und das ausgehärtete Kohlefaserteil vorsichtig aus der Form genommen. Dieser Schritt erfordert Präzision, um eine Beschädigung des Teils zu vermeiden.
7. Veredelung und Inspektion
Der letzte Schritt umfasst die Veredelung und Inspektion. Das Kohlefaserteil wird getrimmt, um überschüssiges Material zu entfernen und die genauen Abmessungen zu erreichen, die erforderlich sind. Anschließend wird es auf Mängel oder Ungereimtheiten überprüft. Zerstörungsfreie Prüfmethoden, wie z. B. die Ultraschallprüfung, werden häufig eingesetzt, um die Integrität des Teils sicherzustellen.

Schlussfolgerung
Die Verwendung eines Autoklaven bei der Herstellung von Kohlefaser-Automobilteilen gewährleistet höchste Qualität und Leistung. Der Prozess umfasst eine sorgfältige Vorbereitung, eine präzise Anwendung von Hitze und Druck sowie eine gründliche Inspektion, was zu Teilen führt, die stark, leicht und ideal für Hochleistungsanwendungen in der Automobilindustrie sind.
WISE hat 12 Jahre Erfahrung im Kohlefaser-Spritzguss, hat eine reiche Technische Reservekönnen Sie uns vertrauen, dass wir Ihr Projekt abwickeln und Anpassen Ihr Produkt.
1. Vorbereiten des Kohlefaser-Layups
Der Prozess beginnt mit der Vorbereitung des Kohlefaser-Layups. Kohlefasergewebe oder Prepreg (mit Harz vorimprägniert) wird je nach Teiledesign in bestimmte Formen und Größen geschnitten. Die Schichten aus Kohlefaser werden sorgfältig in einer Form angeordnet, um die gewünschte Dicke und die gewünschten strukturellen Eigenschaften zu erreichen. Dieser Schritt ist von entscheidender Bedeutung, da er die Festigkeit und Leistung des endgültigen Teils bestimmt.

2. Laden in die Form
Sobald das Kohlefaser-Layup vorbereitet ist, wird es in eine Form gelegt, die die Form des Automobilteils definiert. Die Form ist so konzipiert, dass sie den hohen Drücken und Temperaturen im Autoklaven standhält. Die Kohlefaserschichten werden sorgfältig in der Form positioniert, um eine korrekte Ausrichtung zu gewährleisten und Defekte oder Lufteinschlüsse zu vermeiden.
3. Einlegen in den Autoklaven
Die Form, in der sich das Kohlefaser-Layup befindet, wird dann in den Autoklaven gelegt. Ein Autoklav ist ein Hochdruckbehälter, der gleichzeitig Wärme und Druck ausüben kann. Dieser Schritt ist entscheidend für den Aushärtungsprozess der Kohlefaser.
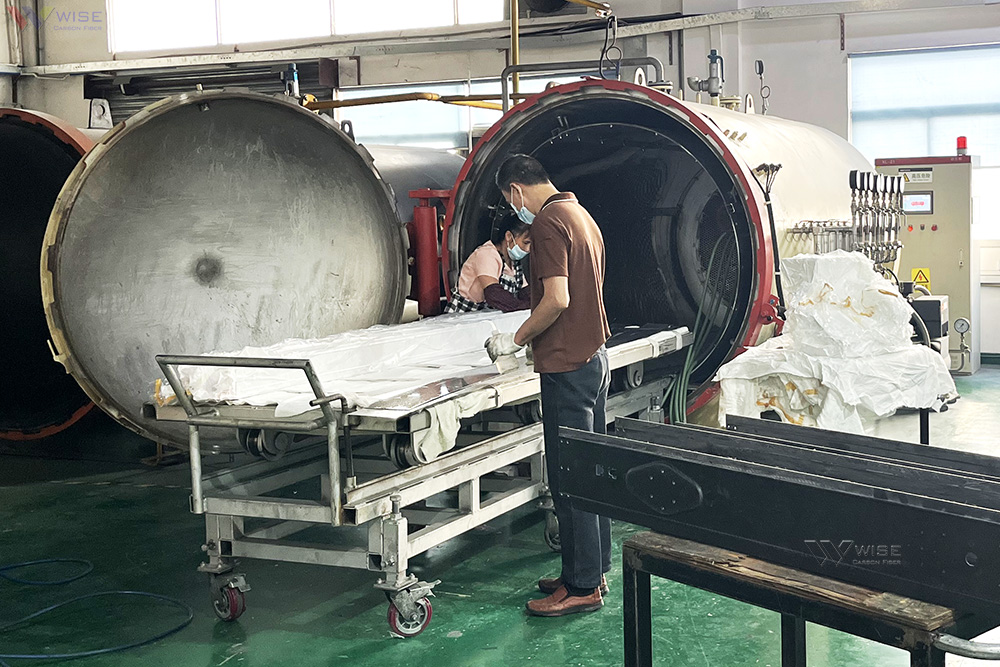
4. Hitze und Druck ausüben
Im Inneren des Autoklaven wird die Temperatur schrittweise auf das erforderliche Niveau erhöht, in der Regel zwischen 120 °C und 180 °C (248 °F bis 356 °F), abhängig vom verwendeten Harzsystem. Der Druck wird ebenfalls erhöht und liegt typischerweise zwischen 50 psi und 100 psi. Die Kombination aus Hitze und Druck lässt das Harz fließen und die Kohlefaser vollständig imprägnieren, wodurch eine starke Verbindung zwischen den Fasern gewährleistet wird.
5. Aushärtungsprozess
Beim Aushärtungsprozess werden Temperatur und Druck für eine bestimmte Dauer, in der Regel mehrere Stunden, aufrechterhalten. Während dieser Zeit durchläuft das Harz eine chemische Reaktion, die dazu führt, dass es aushärtet und aushärtet, wodurch ein fester Verbundwerkstoff entsteht. Die kontrollierte Umgebung im Autoklaven stellt sicher, dass der Aushärtungsprozess gleichmäßig ist, was zu einem qualitativ hochwertigen Teil mit optimalen mechanischen Eigenschaften führt.
6. Kühlen und Entformen
Nach Abschluss des Aushärtungsprozesses wird der Autoklav schrittweise auf Raumtemperatur abgekühlt. Anschließend wird die Form aus dem Autoklaven entnommen und das ausgehärtete Kohlefaserteil vorsichtig aus der Form genommen. Dieser Schritt erfordert Präzision, um eine Beschädigung des Teils zu vermeiden.
7. Veredelung und Inspektion
Der letzte Schritt umfasst die Veredelung und Inspektion. Das Kohlefaserteil wird getrimmt, um überschüssiges Material zu entfernen und die genauen Abmessungen zu erreichen, die erforderlich sind. Anschließend wird es auf Mängel oder Ungereimtheiten überprüft. Zerstörungsfreie Prüfmethoden, wie z. B. die Ultraschallprüfung, werden häufig eingesetzt, um die Integrität des Teils sicherzustellen.

Schlussfolgerung
Die Verwendung eines Autoklaven bei der Herstellung von Kohlefaser-Automobilteilen gewährleistet höchste Qualität und Leistung. Der Prozess umfasst eine sorgfältige Vorbereitung, eine präzise Anwendung von Hitze und Druck sowie eine gründliche Inspektion, was zu Teilen führt, die stark, leicht und ideal für Hochleistungsanwendungen in der Automobilindustrie sind.
WISE hat 12 Jahre Erfahrung im Kohlefaser-Spritzguss, hat eine reiche Technische Reservekönnen Sie uns vertrauen, dass wir Ihr Projekt abwickeln und Anpassen Ihr Produkt.